ФГБОУ ВПО «Северо-Кавказский горно-металлургический институт (государственный технологический университет)»
Сидорчик Елена Владимировна
РАЗРАБОТКА И ИССЛЕДОВАНИЕ МЕТОДОВ И АЛГОРИТМОВ ОПТИМИЗАЦИИ ПРОЦЕССА ОБРАБОТКИ ДЕТАЛЕЙ И ЗАГОТОВОК НА СТАНКАХ С ЧИСЛОВЫМ ПРОГРАММНЫМ УПРАВЛЕНИЕМ
Специальность: 05.13.01 - «Системный анализ, управление и обработка информации (промышленность) по техническим наукам»
Автореферат
Диссертации
на соискание ученой степени кандидата технических наук
ВЛАДИКАВКАЗ - 2014
Научный руководитель: доктор технических наук, профессор
Мустафаев Гусейн Абакарович
Официальные оппоненты:
Ключко Владимир Игнатьевич, доктор технических наук, профессор ФБГОУ ВПО «Кубанский государственный технологический университет», профессор кафедры информационных систем и программирования.
Музаев Илларион Давидович, доктор технических наук, профессор Федеральное бюджетное учреждение науки «Южный математический институт Владикавказского научного центра РАН и Правительства РСО-Алания», ведущий научный сотрудник.
Ведущая организация: ФГБОУ ВПО «Грозненский государственный нефтяной технический университет имени академика М.Д. Миллионщикова».
Защита диссертации состоится 26 сентября 2014 г. в 1500 часов на заседании диссертационного совета Д212.246.01 при ФГБОУ ВПО «Северо-Кавказский горно-металлургический институт (государственный технологический университет)» по адресу: 362021, г. Владикавказ, ул. Николаева, 44, СКГМИ (ГТУ). Факс:(8672) 407-203. E-mail: [email protected].
С диссертацией можно ознакомиться в научно -технической библиотеке ФБГОУ ВПО «СКГМИ (ГТУ)».
А. Ю. Аликов Ученый секретарь диссертационного совета Д212.246.01 к.т.н., доцент
ОБЩАЯ ХАРАКТЕРИСТИКА РАБОТЫ
Актуальность темы исследования. В настоящее время в промышленном производстве широко применяют станки с числовым программным управлением (ЧПУ), в условиях мелкосерийного производства изготавливается 70—75% всей номенклатуры деталей общемашиностроительного применения.
Изыскания и трудоемкий практический опыт влиятельных ученых, в том числе Елиферова В.Г., Горюшкина В.И., Звягинцева Ю.Е., Калянова Г.Н., Пшенникова В.В. свидетельствуют об изменении характеристик процесса резания именно во время механической обработки. Первопричинами нестабильности процесса резания являются нарастающий во времени износ резца, перемена реальных геометрических параметров инструмента, диаметра обработки, жесткости системы резания вдоль обрабатываемой плоскости. Таким образом, применение постоянных режимных условий не могут являться оптимальными на протяжении всего процесса обработки анализируемой плоскости при нестабильных процессах резания.
Недостаток существующих методов создает трудности в решении практической задачи по оптимизации процесса обработки деталей. Все это обуславливает актуальность проведения исследования проблемы повышения эффективности мелкосерийного производства в условиях применения станков с ЧПУ.
Решение данной задачи возможно на основе разработки методов и алгоритмов оптимизации процесса обработки деталей и заготовок на станках с ЧПУ, и является важным научно-прикладным исследованием.
Целью диссертационной работы является разработка методов и алгоритмов оптимизации и повышения эффективности процесса обработки деталей и заготовок на станках с ЧПУ.
Поставленная цель потребовала решения следующих задач:
1. Анализ состояния процесса программируемой обработки деталей и заготовок на станках с числовым программным управлением;
2. Исследование путей повышения эффективности процесса обработки деталей и заготовок на станке с числовым программным управлением;
3. Оптимизация процесса программируемой обработки деталей и заготовок и повышение эффективности обработки деталей на программируемых станках с ЧПУ;
4. Разработка методов и алгоритмов повышения эффективности процесса обработки на станках с числовым программным управлением.
Объект исследования - системы управления обработки информации при программировании процессов обработки деталей на станках с ЧПУ.
Предметом исследования являются модели, методы и алгоритмы, позволяющие повысить эффективность процесса обработки деталей и заготовок на станках с ЧПУ
Методы исследования. Для решения поставленных задач достижения цели исследования использованы: методы системного анализа, методы математического анализа, методы математического моделирования, методы линейного программирования, симплекс-метод.
Научная новизна диссертационной работы состоит в следующем:
1. Разработана математическая модель процесса программируемой обработки деталей на станке с числовым программным управлением, обеспечивающая достижение требуемой точности технологического процесса обработки деталей и заготовок на станке с ЧПУ;
2. Разработаны методы и алгоритмы, позволяющие обеспечить оптимальное управление параметрами для повышения эффективности процесса обработки деталей и заготовок на станках с ЧПУ;
3. Разработаны новые методы контроля и обеспечения точности обработки деталей на станках с ЧПУ, основанные на математических свойствах рассеяния размеров деталей;
4. Предложен подход к определению уровней анализа системы при программировании процесса обработки для станков с ЧПУ, позволяющий оптимизировать эффективность обработки деталей и заготовок на станках с ЧПУ.
Практическая значимость работы состоит в следующем:
1. Реализация разработанных алгоритмов позволяет существенно сократить время простоя станка, обеспечить стабильность качества используемого инструмента, повысить надежность производственной системы за счёт увеличения рационального времени безостановочной и безотказной работы с ЧПУ;
2. Оптимизированы основные этапы программирования процесса обработки деталей и заготовок на станках с ЧПУ с учетом коррекции, возникающей в условиях мелкосерийного производства;
3. Разработанные методы оптимизации программного кода управляющей программы процесса обработки на станках с ЧПУ путем ввода дополнительных параметров обработки, позволяют значительно повысить эффективность работы станка;
4. Результаты диссертации получили внедрение в промышленное производство. Разработанные методы, алгоритмы и комплекс типовых программ приняты к использованию на предприятии ОАО «НПО «Бином» (г. Владикавказ) с экономическим эффектом 683 тыс.рублей. Отдельные материалы и результаты работы используются в учебном процессе СКГМИ (ГТУ).
Реализация результатов работы. Анализ эмпирических данных, полученных по результатам внедрения разработанных методов и средств оптимизации процесса программируемой обработки деталей на станке с ЧПУ, свидетельствует о корректности предложенных подходов к описанию и исследованию системы управления станком и обработки информации линейными моделями, а также об эффективности применения разработанных схем работы на производстве для дальнейшей оптимизации процесса обработки деталей на станках с ЧПУ.
Обоснованность и достоверность научных положений обеспечивается полученными в ходе вычислений и многочисленных экспериментальных исследований результатами, соответствием полученных результатов, как в ходе теоретических, так и в ходе экспериментальных исследований, а также положительными данными практических результатов внедрения научных исследований в реальное промышленное производство.
На защиту выносятся:
1. Математическая модель процесса обработки деталей на станке с числовым программным управлением, обеспечивающая достижение требуемой точности технологического процесса обработки деталей и заготовок на станке с ЧПУ;
2. Методы и алгоритмы, позволяющие обеспечить оптимальное управление параметрами, выбор наиболее оптимальных параметров
управления системы процессов обработки (резания), который обеспечивает повышение эффективности процесса обработки деталей и заготовок на станках с ЧПУ;
3. Методы контроля и обеспечения точности программируемой обработки деталей на станках с ЧПУ, основанные на математических свойствах рассеяния размеров деталей;
4. Основные уровни анализа системы при программировании процесса обработки деталей и заготовок на станках с ЧПУ с учетом коррекции, возникающей в условиях мелкосерийного производства;
5. Методы и алгоритм: оптимизации программного кода управляющей программы процесса обработки на станках с ЧПУ путем ввода дополнительных параметров обработки, позволяющих значительно повысить эффективность работы станка.
Апробация работы. Основные положения и результаты работы докладывались и обсуждались на III Международной заочной научно-практической конференции «Наука вчера, сегодня, завтра» (21.08.2013), г. Новосибирск, II Международной научно-практической конференции «Актуальные проблемы современной науки в 21 веке» (30.08.2013), г. Махачкала, X Международной научно-практической конференции «Техника и технология: новые перспективы развития» (28.08.2013), Естественные и технические науки, г. Москва.
Публикации. Основные результаты диссертационного исследования опубликованы в 13 печатных трудах, из них 3 в изданиях, которые входят в перечень рекомендованных ВАК РФ.
Личный вклад. Все результаты, составляющие основное содержание диссертационной работы получены автором самостоятельно.
Структура и объем работы Диссертационная работа состоит из введения, четырех глав и заключения, содержит 221 страниц машинописного текста, 57 рисунков, 13 таблиц, 12 приложений. Список литературы состоит из 98 наименований.
ОСНОВНОЕ СОДЕРЖАНИЕ РАБОТЫ
Во введении обоснована актуальность темы исследования, сформулированы цель и задачи исследования, раскрыта научная новизна, отмечена практическая значимость и дана апробация полученных результатов работы.
В первой главе рассмотрено современное состояние вопроса оптимизации процесса обработки деталей и заготовок на станке с числовым программным управлением (ЧПУ), проведен анализ основных требований к процессу обработки деталей на станках с ЧПУ в условиях мелкосерийного производства.
Определены основные показатели эффективности процесса обработки деталей и заготовок на станках с ЧПУ, в том числе зависимость эффективности применения программного управления станком от концентрации и сложности процесса обработки детали на станке. Для получения изделий правильных размеров и формы относительное положение всех элементов системы СПИД (станок—приспособление—инструмент— деталь) должно быть увязано между собой. Такую размерную увязку следует выполнять в системе координат станка, инструмента, детали непосредственно при программировании кода управляющей программы.
На основе предложенных ранее моделей процессов мелкосерийного производства уточнена функциональная схема управления станком с ЧПУ, которая приведена на
рисунке 1, проведен анализ существующих проблем бесперебойной работы на станках с ЧПУ и возможных способов их решения, выделены основные проблемы работы промышленных производств, определены этапы программирования управляющего кода для правильного процесса обработки деталей и заготовок на станках с ЧПУ. На схеме показаны связи кода управляющей программы (УП) с управлением ЧПУ, системным программным обеспечением (СПО) и станком.
Определены типичные ошибки, возникающие при подготовке программ для станков с ЧПУ на каждом из этапов подготовки процесса обработки, причины таких ошибок и мероприятия, необходимые для их устранения, проведен анализ основных критериев выбора параметров режимов резания, обеспечивающие оптимальную стойкость инструмента, определены основные принципы, применяемые при выборе параметров режима процесса резания при токарной обработке на станке с ЧПУ с учетом особенностей конструктивных и технологических параметров обрабатываемой детали.
Определена последовательность выбора параметров режима резания для токарных станков с ЧПУ для заданных условий обработки.
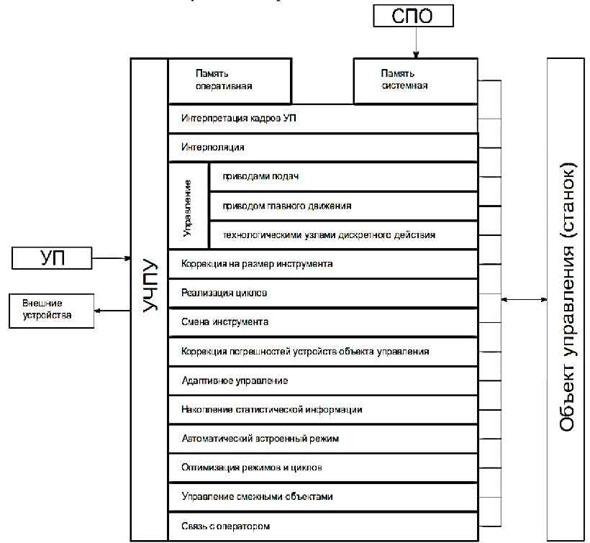
Рисунок 1 - Функциональная схема управления станком с числовым программным управлением
Во второй главе проведено исследование путей повышения эффективности процесса обработки на станке с числовым программным управлением. Повышение производительности обеспечивает компенсацию больших затрат, связанных с высокой себестоимостью оборудования с ЧПУ. Поэтому первоначально необходимо производить выбор номенклатуры деталей для их программной обработки на станке с ЧПУ, что показано на
рисунке 2.
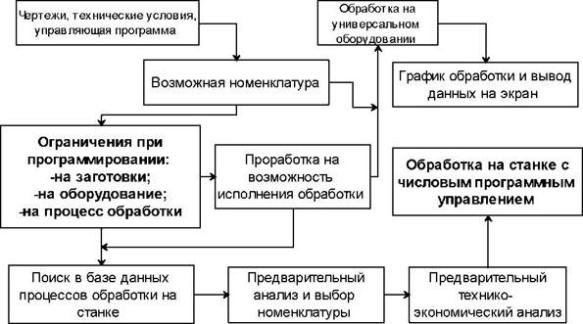
Рисунок 2 - Функциональная схема алгоритма для выбора номенклатуры деталей при обработке их на станке с числовым программным управлением
Структурно процесс программирования также делится на операции, элементами которых являются установки, позиции, технологический и вспомогательный переходы, рабочие и вспомогательные ходы. Детализация процесса обработки деталей для оборудования с ЧПУ приводит к разделению ходов на шаги, каждый из шагов представляет собой перемещение на участке траектории инструмента.
При оптимизации процессов обработки деталей на станках с ЧПУ необходимо выполнение следующих требований:
- унификация внутренних и наружных радиусов;
- унификация элементов форм деталей и их размеров;
- создание конфигурации детали, обеспечивающей свободный доступ инструмента для обработки поверхностей;
- обеспечение возможности надежного и удобного базирования детали при обработке.
Все эти требования прежде всего направлены на сокращение затрат рабочего времени процесса программируемой обработки детали на станке с ЧПУ: уменьшение типовых размеров применяемого режущего инструмента, использование более производительного (экономически выгодного) инструмента, замену специального инструмента стандартным, уменьшение числа переустановок детали, снижение количества и стоимости требуемой оснастки, повышение точности базирования, а также точности и производительности обработки, уменьшение степени коробления детали при обработке и объема последующей слесарной (станочной) ручной доработки, сокращение затрат на расчет и подготовку управляющих программ (УП).
На сегодняшний день при обработке на станке с ЧПУ при точении или резании характерна автоматизированная система управления, то есть каждая система числового программного управления построена на базе постпроцессоров (микропроцессорных точных систем), которые зачастую обладают не только необходимыми, но и избыточными мощностями вычисления. Стоит отметить, что, несмотря на это определяются и корректируются режимы резания до сих пор вручную, программа в системе ЧПУ подвергается ручному анализу и редактированию. Прежде всего, это связывается с тем, что все существующие на настоящий момент времени методы и способы подготовки технологической информации практически не поддаются ее последующей формализации, а также зачастую дают не совсем точные результаты, следовательно, требуют последующего исправления и корректировки.
Причиной такой недостаточной достоверности данных в основных процессах токарной работы математических моделей обработки на станке с ЧПУ является большая неточность наиболее важных зависимостей, используемых для расчета скорости и сил резания. Применяемые на большинстве производств
алгоритмы и используемые программы автоматизированного расчета режимов обработки на ЭВМ не могут дать точных результатов в силу того, что точно не бывают учтены реальные условия обработки, материал и состояние детали и инструмента.
Таким образом, в ходе исследования, разработан алгоритм решения задачи линейного программирования симплекс-методом при выборе наиболее оптимальных параметров управления процессом программируемой обработки для повышения эффективности. По этой проблеме предложены и используются для расчета оптимальной обработки модели, которые основаны на применении мониторинга размера, замеряемого непосредственно в процессе обработки материала в зоне резания. Замеряемый параметр точности обработки детали и инструмента является наиболее полным показателем технологических свойств основных контактирующих друг с другом материалов детали и инструмента. На этой основе предлагаются модели для определения сил резания и скорости:
Vрез = (W - tKпр)/ p0.2l0.15F0.35KSпр
где Kпр - коэффициент эффективности пробного прохода;
W, t, s - коэффициенты условия предварительной обработки,
(W = 625; t = 24,7; s = 0,24);
Р - принятая за норму стойкость инструмента, мин; l - глубина резания, мм;
F - величина подачи, мм/об;
Ах = (Wx + txКпр)l1F0.5V-0.4рез,
Аy = (Wy + tyКпр)l0.9F0.6V-0.3рез,
Аz = (Wz + tzКпр)l0.75F0.75V-0.15рез,
Аx, Ay,
Az — составляющие силы резания, кгс; l - глубина резания, мм;
F -величина подачи, мм/об; Vрез - скорость резания, м/мин;
Кпр - коэффициент эффективности пробного прохода;
Wx, Wy, Wz
- постоянные величины, соответственно равные 360; 300; 320; tx,
ty,
tz - постоянные величины, соответственно равные 7; 10; 5,5; - используемые коэффициенты, которые определены из частичных условий предварительной обработки.
В соответствии с проведенными исследования в условиях промышленного производства, данные модели могут обеспечить более точное соблюдение надежного заданного периода полной стойкости режущего инструмента. Следовательно, созданы предпосылки для использования указанных моделей в алгоритме технологических процессов для расчета режимов резания при обработке на станке с числовым программным управлением.
Математическое обоснование и формулировка получения решения задачи при выборе наиболее оптимальных параметров управления системы процессов обработки (резания), как задачи линейного программирования, определяется следующим. Найти
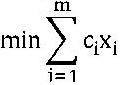
при выполнении ограничений
xi ≥
0, і = 1,m
і = 1,n
где m - число параметров управления или переменных;
n - число ограничений задачи; аij,
bj - константы.
Если нагружать технологическую систему составляющей силы резания Ру, что показано на
рисунке 3 и измерять возникающие деформации у (деформацию детали деформацию элементов станка
уд, деформацию элементов приспособления упр, деформацию инструмента
уи), то можно установить некоторую, чаще всего нелинейную зависимость
Ру=f(х) деформации элементов системы СПИД от силы нагружения, которая показана кривыми 1 на рисунке 3.
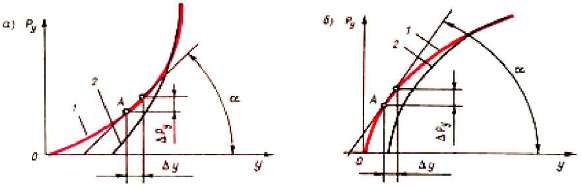
Рисунок 3 - Влияние упругих деформаций системы СПИД на точность обработки в условиях мелкосерийного производства на станке с числовым программным управлением
В качестве критерия жесткости принято отношение приращения
ΔРу радиальной составляющей силы резания, направленной по нормали к обрабатываемой поверхности, к приращению
Δy, отсчитанной в том же направлении деформации режущей кромки инструмента относительно поверхности детали:
j =
ΔРу/Δy,
где j — в Н/м;
ΔРу
— в Н;
Δy — в мм. Для оценки жесткости в любой точке
А кривой Ру = f(x) находят производную в данной точке
y' = jA = dPy/dy. Численно производная равна
tan a, где
a — угол наклона касательной к кривой в точке
A, что показано на рисунке 3.
Кривые разгрузки 2 чаще всего не совпадают с кривыми нагрузки 1, а площадь, заключенная между ними, отражает работу сил трения.
Если в двухкоординатной системе XZ неравномерность на каждый оборот ходового винта проявляется при движении по координате
Z, а движение по координате X осуществляется равномерно, как показано на
рисунке 4, обозначение Pz и
Рх - шаги ходовых винтов соответственно по осям
Z и X).
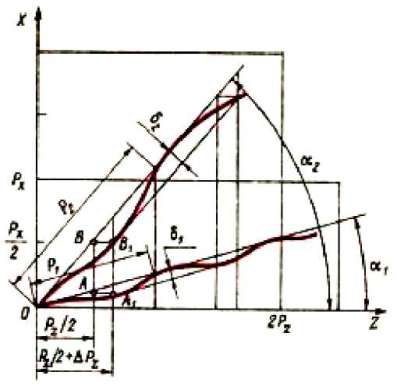
Рисунок 4 - Схема возникновения погрешности в
режиме линейной интерполяции при обработке детали на станке с числовым
программным управлением
Выполняется линейная интерполяция - протачивание конической поверхности на токарном станке под углом
ai к продольной оси
Z.
В связи с цикличностью ошибки по оси Z через полоборота ходового винта каретка пройдет путь, больший, чем половина шага, на некоторую величину
ΔРz, и рабочий орган вместо точки
А окажется в точке А1. На обработанной поверхности возникает волнистость с высотой волны
δ1 =
ΔPZ sina1 и шагом
Р1 = Pz/cosa1.
С увеличением угла наклона траектории к оси Z увеличиваются высота
δ2 =
ΔPZ sina2
и длина Р2 = Pz/cosa2 волны. Тогда оценивая шаг и высоту волны на обработанной поверхности, можно выявить элемент или группу элементов, порождающих циклическую погрешность перемещения двух поверхностей под углами a1
и a2. При этом необходимо показать, что если при малом угле наклона траектории к одной из осей (угол a1) высота и шаг
Р1 волны меньше, чем
δ2 и Р2
при большом угле a2, то основное воздействие на погрешность оказывают элементы привода, расположенные и работающие по той же оси. Если элемент, порождающий ошибку, связан с ходовым винтом зубчатыми передачами с коэффициентом редукции
i, то проекция волны на ось будет иметь шаг, равный Рі.
Целевая функция. Для повышения эффективности в нашем случае следует принимать основное время технологической обработки (величину, обратную
mF) в качестве критерия оптимальности:
tосн = 1/mF; mF
® max
При условии, что оптимальный период стойкости резца (инструмента) P
не менее установленного, а значение ряда технологических характеристик и параметров процесса обработки не больше установленных в программе предельных значений.
Математическая модель для оптимального режима обработки содержит в себе систему технологических ограничений, которые выражены в виде ряда линейных неравенств, а также линейное уравнение целевой функции. Необходимо все указанные технологические ограничения привести путем логарифмирования к линейному виду.
Предложена последовательность выбора параметров режима резания для токарных станков с ЧПУ (для заданных условий обработки): глубина резания; подача; стойкость режущего инструмента; скорость резания.
Показано, что оптимальный режим программируемой обработки детали и заготовки на металлорежущем токарном станке с числовым программным управлением зависит от технологических свойств заготовки и свойств режущего инструмента. Системный анализ свойств системы «чертеж - программный код - станок - инструмент - деталь» позволяет обозначить оптимальные подачу и скорость резания, которые обеспечивают технологическое формообразование заготовки или детали в соответствии с требуемыми техническими условиями при наименьших затратах производительности труда. Каждое из ограничений представляется в следующем виде:
x1iln(100F) +x2iln(m) = bi
То есть мы получаем систему линейных алгебраических уравнений, которые ограничивают область допустимых значений
m и F:
ln(100F) ≥ b1 (1)
ln(100F) ≤ b2 (2)
ln(m) ≥ b3 (3)
ln(m) ≤ b4 (4)
ln(m) + 0.35 ln(100F)
≤ b5 (5)
ln(m)
≥ b6 (6)
-0.15ln(m) + 0.75ln(100F)
≤ b7 (7)
ln(m) + ln(100F) ≤ b8 (8)
-0.15ln(m) + 0.75ln(100F)
≤ b9 (9)
-0.15ln(m) + 0.75 ln(100F)
≤ b10 (10)
-0.3ln(m) + 0.6 ln(100F)
≤ b11 (11)
Wln(m) + ln(100F)
≤ b12 (12)
Также определены математические зависимости, для технических ограничений, которые непосредственно влияют на оптимальность режимов программируемой обработки. Систему ограничений можно представить графически на
рисунке 5, где область значений F и
т обозначена редкой штриховкой, которая допустима техническими характеристиками кинематики станка.
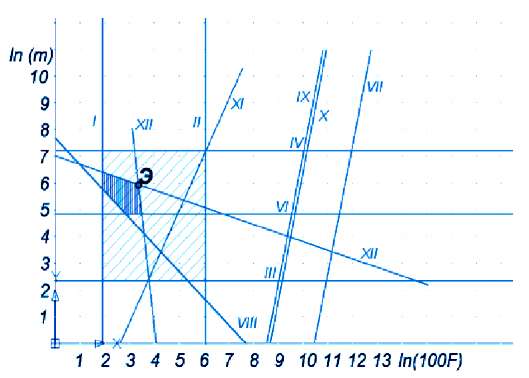
Рисунок 5 - График зависимостей технологических ограничений при программируемой обработке на станке с числовым программным управлением
Частая штриховка - область значений F и т, которая удовлетворяет всем техническим ограничениям.
В этом случае граничной прямой, определяющей полуплоскость, в которой возможны решения систем неравенств, представляется каждое из технологических ограничений.
Величина для ограничений V, VII, IХ-ХII определяет оптимальный коэффициент эффективности обработки на станке с ЧПУ. В процессе обработки он меняется, а, следовательно, должны изменяться также границы исследуемой области.
Эффективной возможностью решения такой задачи, которая связаны с повышением эффективности и с поиском оптимальных значений нескольких параметров процесса обработки, является симплекс-метод, автоматизированным способом реализуемый с помощью
ЭВМ. Симплекс-метод один из наиболее распространенных и отработанных методов решения задачи линейного программирования. Симплекс-метод позволяет найти вершину многогранника (крайнюю точку исследуемой допустимой области), а также определить является ли найденная точка экстремумом целевой функции. Именно такая конечность симплекс-метода является его важной особенностью, потому что методы решения задач нелинейного программирования дают приближенные значения, то есть не являются конечными.
В ходе исследования с помощью программного обеспечения MathCad был разработан и смоделирован процесс обработки, а также определены крайние точки экстремума исходной целевой функции. Основываясь на полученных данных предложен метод перенастройки и поднастройки некоторых параметров программируемого процесса обработки на станке с ЧПУ, рассчитаны оптимальные значения величин
Дт и ДА, которые способствуют корректировке исходных параметров в программном коде обработки детали, используя коэффициент эффективности как интегральный показатель совместимости кинематико - механических свойств при составлении кода управляющей программы.
Применение предложенных алгоритмов и разработанной математической модели как решение задачи линейного программирования путем достижения высокой точности конечных данных с помощью отработанного симплекс-метода, реализация алгоритмов управления системой обработки на станке с ЧПУ на производстве позволяет существенно уменьшить технологическое время обработки, а особенно, операций точения.
Реализация алгоритма разработанной математической модели позволяет сократить также время простоя, которое может быть связано с поломкой инструмента, значительно повысить надежность производственной системы за счет непосредственного увеличения рационального времени безостановочной и безотказной работы станка с ЧПУ.
На основе предложенной математической модели разработан алгоритм решения задачи линейного программирования для обработки деталей по технологическим возможностям станка и трудоемкости составления программного кода для изготовления детали, представленный на
рисунке 6, а как следствие задача подбора наиболее оптимальных параметров режима обработки для современной высокоточной системы ЧПУ.
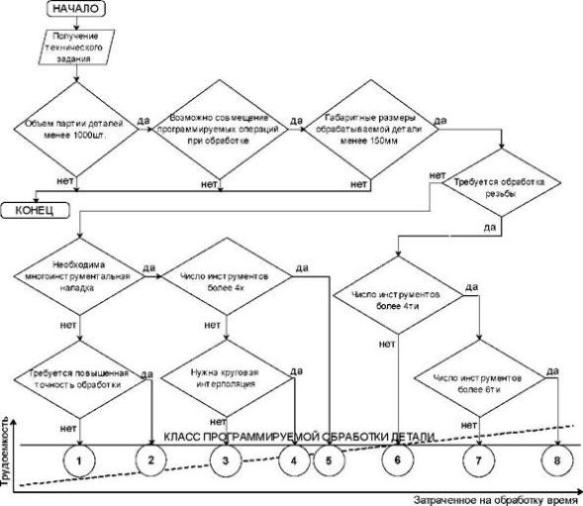
Рисунок 6 - Алгоритм построения классификационного ряда поправки для обработки деталей по технологическим возможностям станка и трудоемкости составления программного кода для изготовления детали в условиях мелкосерийного производства
В диссертационной работе разработана математическая модель процесса обработки деталей на станках с ЧПУ для достижения высокой точности, которая в соответствии с проведенными исследованиями в условиях промышленного производства может обеспечить точное соблюдение надежного заданного периода полной стойкости режущего инструмента.
В ходе исследования определены основные требования к оптимизации процессов обработки деталей на станках с ЧПУ или намеченных к обработке. Сформированы элементы структуры типового и группового технологических процессов, определены основные факторы, влияющие на точность обработки, и факторы, влияющие на точность системы управления процессом обработки деталей, что позволяет уменьшить общую систематическую погрешность процесса обработки деталей и заготовок. Точность обработки зависит от суммарной погрешности, поэтому станок с ЧПУ должен обеспечить ее, работая в автоматическом или в полуавтоматическом режиме.
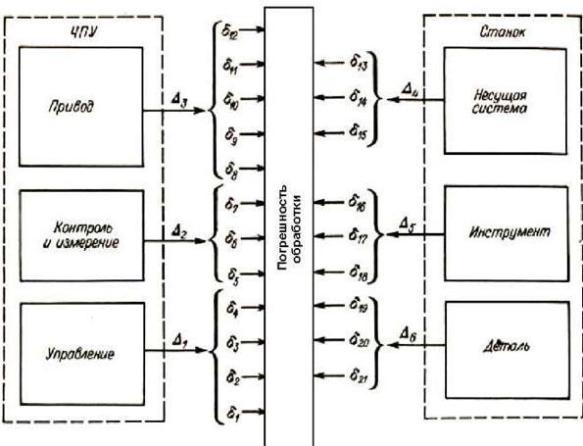
Рисунок 7 - Суммарная погрешность обработки деталей и заготовок на станках с числовым программным управлением
δ1, δ2,
δ3,
δ4 -
ошибки программирования, интерполятора, корректоров интерполятора и
формирования команды « выход в нуль»;
δ5,
δ6 - ошибки датчика - внутришаговая и накопленная;
δ7 - ошибка нормирующего преобразователя;
δ8 - ошибка дрейфа характеристик привода;
δ9,
δ10, δ11 - ошибки привода - динамическая, моментная скоростная;
δ12 - ошибка шариковой винтовой пары;
δ13 - геометрическая ошибка станка;
δ14,
δ15 - упругие перемещения соответственно станка и приспособления;
δ16 - размерная ошибка установки инструмента;
δ17 - износ инструмента;
δ18 - упругие деформации инструмента;
δ19 - геометрическая ошибка установки детали;
δ20 - упругое перемещения детали;
δ21 - температурная деформация детали.
В работе разработаны новые методы контроля точности обработки деталей на станках с ЧПУ, основанные на математических свойствах рассеяния размеров деталей, обработанных при неизменных условиях и расположенных в возрастающем порядке с указанием частоты повторения и распределением размеров заготовок.
Нормативы точности линейного позиционирования рабочих органов станков с ЧПУ приведены в
таблице 1 (погрешность а относится осям X,
У,
W, R, погрешность
δ — к оси
Z).
На суммарную погрешность обработки влияет ряд факторов, представленных на
рисунке 7:
- точность станка,
- жесткость системы СПИД,
- точность системы управления,
- погрешности наладки инструментов на размер,
- погрешности установки заготовки, погрешности изготовления инструмента,
- размерный износ режущего инструмента.
Таблица 1 - Допускаемая накопительная погрешность А при одностороннем подходе к заданной координате, мкм
Класс точности станка |
Перемещения по длине, мм |
До 50 |
Св.50 до 80 |
Св.80 до 125 |
Св.125 до 200 |
Св.200 до 320 |
Св.320 до 500 |
Св.500 до 800 |
Св.800 до 1250 |
Св.1250 до 2000 |
а |
б |
а |
б |
а |
б |
а |
б |
а |
б |
а |
б |
а |
б |
а |
б |
а |
б |
Н (1-3) |
8 |
12 |
10 |
10 |
12 |
20 |
16 |
25 |
20 |
30 |
25 |
40 |
40 |
50 |
40 |
65 |
50 |
80 |
П (4-6) |
4 |
6 |
5 |
8 |
6 |
10 |
8 |
12 |
10 |
16 |
12 |
20 |
16 |
26 |
20 |
30 |
25 |
40 |
В (7-8) |
2 |
3 |
2,5 |
4 |
3 |
5 |
4 |
6 |
5 |
8 |
6 |
10 |
8 |
12 |
10 |
16 |
12 |
20 |
В таблице 2 (погрешность а относится осям X, У,
W, R, погрешность
δ — к оси
Z) приведены предельные допускаемые значения нестабильности при линейном позиционировании.
Таблица 2 - Допускаемая нестабильность
δ достижения заданного положения при позиционирования, мкм
Класс точности станка |
Перемещения по длине, мм |
До 50 |
Св.50 до 125 |
Св.125 до 320 |
Св.320 до 800 |
Св.800 до 2000 |
а |
б |
а |
б |
а |
б |
а |
б |
а |
б |
Н(1-3) |
9,6 |
15,0 |
12,0 |
18,0 |
15,0 |
24,0 |
24,0 |
36,0 |
36,0 |
60,0 |
П (4-6) |
4,8 |
7,2 |
6,0 |
9,6 |
7,2 |
12,0 |
12,0 |
18,0 |
18,0 |
30,0 |
В (7-8) |
2,4 |
3,6 |
3,0 |
3,8 |
3,6 |
6,0 |
6,0 |
9,6 |
9,6 |
15,0 |
Общая допускаемая ошибка при позиционировании рабочих органов
∆р=
∆ +
δ. Для сохранения точности станка в течение длительного времени эксплуатации нормы геометрической точности при изготовлении станка по сравнению с нормативными следует ужесточать на 40%. Таким образом, завод-изготовитель может резервировать в новом станке запас на изнашивание.
Разработаны также новые методы обеспечения точности обработки деталей на станках с ЧПУ, которые позволяют достигнуть заданную точность обработки заготовок и деталей на станках с ЧПУ.
Третья глава посвящена повышению эффективности обработки деталей на программируемых станках с ЧПУ, определены основные критерии для повышения эффективности и производительности обработки деталей и заготовок на станках с ЧПУ, разработана система технологической подготовки производства с целью повышения эффективности промышленного производства, что позволяет получить повышение экономического эффекта.
Показано, что реализация алгоритма разработанной математической модели позволяет существенно сократит время простоя станка, значительно повысить надежность производственной системы, а также способствует значительному повышению качества обработки деталей. Для учета простоев составлена и закодирована классификация простоев: организационных и технических Наблюдения показали, что простои станков и систем составляют от 26 до 35%. Основными причинами технических простоев являются: наладка станка (53,01% времени технических простоев), неисправность станка и его электрооборудования (23,47%), неисправность устройства ЧПУ (14,38%). Среднее время восстановления находится в пределах 1,34 ч.
Разработана методика, содержащая основные данные процесса обработки деталей и заготовок на станке, предложены методы, которые являются эффективным способом повышения производительности процесса обработки деталей и заготовок на станках с ЧПУ, описаны преимущества при возможности многостаночного обслуживания.
Рассеяние размеров деталей приведено в таблице 3, обработанных на налаженном станке, и закономерность этого рассеяния могут быть установлены на основе закона больших чисел при помощи кривых распределения. После измерения 350 заготовок с действительными размерами в пределах 49,940— 50,000 мм распределение их размеров имеет вид, приведенный в таблице 3.
Таблица 3 - Распределение размеров обработанных заготовок в партии
Номер
группы |
Интервал размеров, мм |
Частота повторения, т |
Частость, т/п |
1 |
49,940-49,946 |
8 |
0,023 |
2 |
49,946-49,952 |
16 |
0,046 |
3 |
49,952-49,958 |
25 |
0,071 |
4 |
49,958-49,964 |
65 |
0,186 |
5 |
49,964-49,970 |
85 |
0,242 |
6 |
49,970-49,976 |
73 |
0,208 |
7 |
49,976-49,982 |
48 |
0,137 |
8 |
49,982-49,988 |
24 |
0,069 |
9 |
49,988-49,994 |
6 |
0,017 |
10 |
49,994-50,000 |
2 |
0,001 |
По результатам исследования построены кривые распределения: композиция нормального закона и закона равной вероятности, которая найдена методами математической статистики, представлены на
рисунке 8.
Рисунок 8: Распределение размеров обработанных
заготовок в партии. 1 - действительное распределение; 2 - кривая нормального распределения
Если одновременно воздействуют при обработке на заготовки разные факторы, то возникают как систематические, так и случайные погрешности, подчиняющиеся разным законам.
Уравнение кривой нормального распределения при обработке детали на станке с ЧПУ имеет вид:
у= φ(х) =
σ-1(2π)-1/2ехр[—х2/(2σ2)]
где у — частота появления погрешности; х — отклонение действительных размеров от средних,
х = Li — Lср,
σ — среднеквадратическое отклонение аргумента, равное квадратному корню из средней арифметической квадратов отклонений
(Li — полученные размеры; Lср
— среднее арифметическое действительных размеров заготовок).
Средний размер детали в партии Lср(мм) равен среднему арифметическому из размеров всех деталей всех групп:
Lср = (m1L1 + m2L2
+ ... + mkLk)/n =
где m1, m2, ... ,
mк — частота (количество деталей в каждой группе);
n = m1 + m2 + ... + mк
— общее количество измеренных деталей в партии; L1,
Lср — размеры отдельных групп деталей, соответствующие числу интервалов;
к — число групп, соответствующее числу интервалов.
Среднеквадратическое отклонение определяют по формуле:
σ = {[((m1х2
+ m2х2 + ... + mкх2к)/n]1/2 = {[(m1(L1
- Lcр)2 + m2(L2 - Lcр)2 +
... + mk(Lk - Lcр)2)/n]} = [ ]
где х1 = L1 — Lср; х2 =
L2 — Lср; ...; хк = Lк —
Lср; — отклонения действительных размеров от среднего арифметического в каждой группе деталей.
Параметр Lср (математическое ожидание) определяет центр группирования размеров, параметр
σ — рассеяние их относительно центра.
Анализ уравнения показывает, что кривая нормального распределения симметрична относительно оси ординат.
При Li = Lср = 0 кривая имеет максимум:
уmах =
σ-1(2π)-1/2
≈ 0,4/σ
На расстоянии ±σ от вершины кривая имеет две точки перегиба (А и
В) с ординатами
ya = yв = σ-1(2π)-1/2 = уmахе-1/2 = 0,6уmах = 0,24/σ.
Кривая асимптотически приближается к оси абсцисс. Отклонения действительных размеров от среднего размера почти для всех обработанных деталей находятся в пределах от
+3σ до
—Зσ, т. е. абсолютное значение отклонения равно
6σ. Если допуск на обработку больше
6σ, то поле рассеяния размеров и погрешность обработки меньше допуска, то есть все детали по размерам годные, как показано на рисунке 8. В ходе исследования предложена функциональная схема процесса обработки информации в системе «чертеж-деталь», которые позволят уточнить основные направления и пути повышения эффективности обработки деталей и заготовок на станках с ЧПУ, определить необходимое и достаточное условие получения оптимального эффекта с учетом правильного подбора детали - объекта обработки. Определены этапы обработки информации на всех уровнях технологического программирования, а также рассчитаны затраты времени по этапам и пути их уменьшения. Определены факторы, обеспечивающие минимизацию потерь при обработке деталей на станках с ЧПУ и существенного повышения эффективности процесса обработки.
В четвертой главе разработаны методы и алгоритмы повышения эффективности процесса обработки деталей и заготовок на станках с ЧПУ.
Предложен новый подход к определению уровней анализа системы при программировании процесса обработки для станков с ЧПУ, позволяющий оптимизировать эффективность обработки деталей и заготовок на станках с ЧПУ на основе разработанной математической модели.
Процесс подготовки управляющей программы (УП) можно представить как последовательное программирование отдельных этапов обработки детали в
таблице 4.
При ручном программировании самым главным является характер представления и организации информации УП в принятом коде.
Таблица 4 - Уточненные уровни автоматизации при программировании обработки для станков с числовым программным управлением
Этап
подготовки
УП |
Задачи подготовки УП |
Уровень
автоматизации |
1 |
2 |
3 |
4 |
I |
Разделение операции на установку и позиции |
- |
- |
- |
+ |
|
Выбор метода крепления заготовки |
- |
- |
- |
+ |
|
Подготовка операционной карты |
- |
- |
- |
+ |
II |
Определение последовательности переходов |
- |
- |
- |
+ |
|
Выбор инструмента |
- |
- |
- |
+ |
|
Разделение переходов на ходы |
- |
- |
+ |
+ |
|
Расчет режимов обработки |
- |
- |
+ |
+ |
|
Подготовка карт наладки станка и инструмента |
- |
- |
+ |
+ |
III |
Определение наладочных размеров инструмента и |
- |
- |
+ |
+ |
|
оборудования |
- |
- |
+ |
+ |
|
Пересчет размеров детали в координаты опорных |
- |
+ |
+ |
+ |
|
точек траектории |
- |
+ |
+ |
+ |
|
Расчет координат опорных точек |
|
|
|
|
|
Преобразование систем координат |
|
|
|
|
IV |
Формирование элементарных перемещений |
- |
+ |
+ |
+ |
|
Определение технологических команд |
- |
+ |
+ |
+ |
|
Кодирование УП |
+ |
+ |
+ |
+ |
|
Запись УП на программоноситель |
+ |
+ |
+ |
+ |
V |
Контроль программоносителя |
+ |
+ |
+ |
+ |
|
Контроль траектории инструмента |
+ |
+ |
+ |
+ |
|
Редактирование УП |
+ |
+ |
+ |
+ |
Методика подготовки УП, включая их редактирование, зависит также от типа УЧПУ станка, конкретных условий производства, организационных принципов работы станка с ЧПУ и др. В процессе исследования разработан алгоритм для оптимизации процесса обработки деталей на станке с ЧПУ, а именно алгоритм загрузки инструмента при программировании управляющей программы процесса обработки, который показан на
рисунке 9.
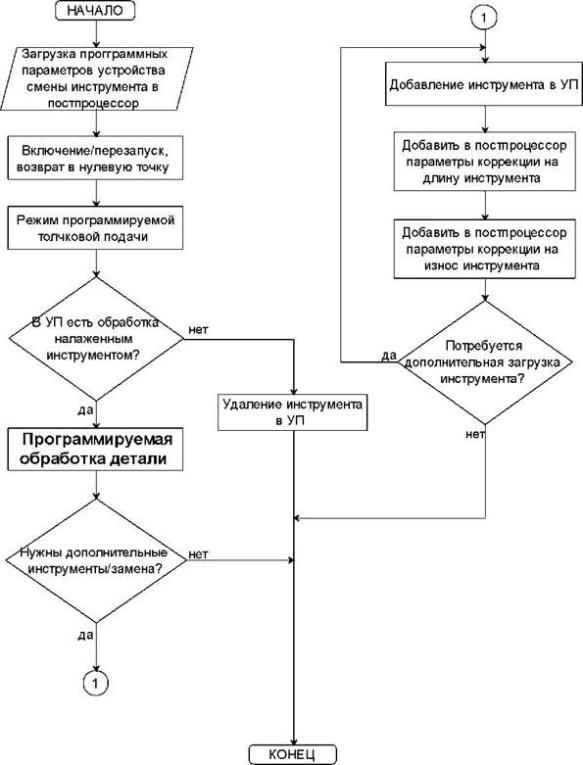
Рисунок 9 - Блок-схема алгоритма загрузки инструмента при программировании управляющей программы процесса обработки
Оптимизирован процесс коррекции геометрии инструмента и установка коррекции инструмента при помощи ручного программирования, описана схема настройки коррекции параметров инструмента, предложены рекомендации для правильного подбора инструмента для обработки детали на станке с ЧПУ. Резание не должно выполняться во время хода или выхода в режим коррекции на фрезу или перехода с коррекции одной стороны на другую. Аналогично, при переходе от коррекции левой стороны к коррекции правой и обратно, начальная точка хода, который должен поменять направление коррекции на фрезу, будет скорректирована в одну сторону от запрограммированного пути. Коррекция на режущую кромку инструмента сдвигает запрограммированный путь инструмента, таким образом, чтобы осевая линия инструмента сместилась влево или вправо от запрограммированного пути.
Конечная точка при этом будет скорректирована в другую сторону от запрограммированного пути по алгоритму оптимизации обработки деталей и заготовок на станках с числовым программным управлением путем коррекции при программировании и обработке по первой детали назначения переходов, который показан на рисунке 10. Поэтому инструмент будет двигаться по пути, который не будет совпадать с запланированным путем или направлением.
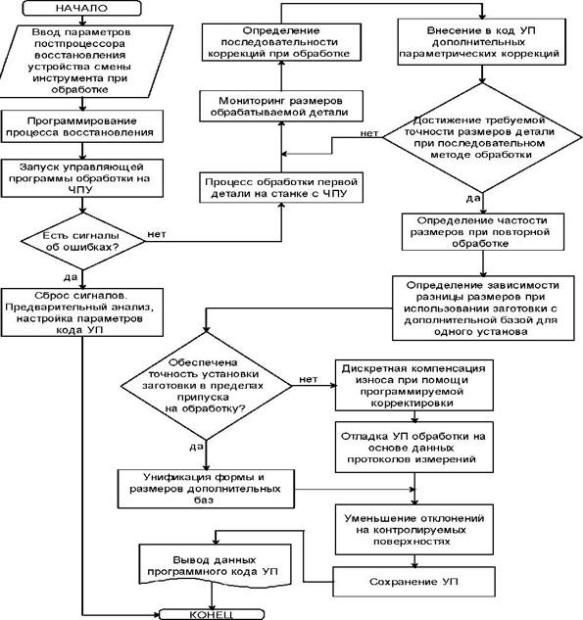
Рисунок 10 - Блок-схема алгоритма оптимизации обработки деталей и заготовок на станках с числовым программным управлением путем коррекции при программировании и обработке первой детали
При последовательном включении коррекции на режущий инструмент в линейном перемещении, за которым следует второе перемещение на угол менее 90°, существуют два способа для точного вычисления перемещения: тип А или тип В.
Коррекция на режущую кромку резца применяется при изменении радиуса вершины резца, а также при износе, проявляющемся в образовании в процессе резания криволинейных и конических поверхностей.
Первый тип вычисления - А - непосредственно перемещает инструмент в начальную точку коррекции режимов второго прохода. Схемы иллюстрируют существенные различия между двумя типами А и В для параметров настройки Fanuc и для параметров настройки Yasnac.
Коррекция на режущую кромку резца позволяет вносить в программную траекторию инструмента поправки, учитывающие размеры разных инструментов и их износ. Разработан алгоритм назначения переходов обработки отверстий на токарном станке с числовым программным управлением для выбора блока подпрограмм процесса обработки, показанный на рисунке 11. Оператор станка может сделать это, вводя минимальные данные коррекции во время выполнения без дополнительных действий по программированию.
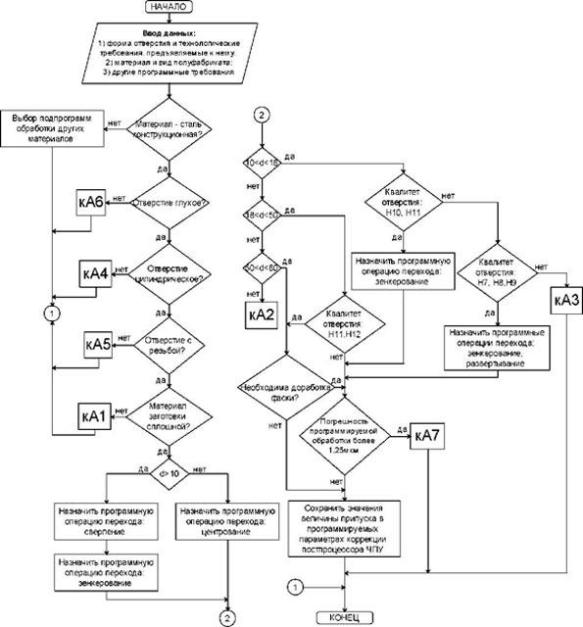
Рисунок 11 - Блок-схема алгоритма назначения переходов обработки отверстий на токарном станке с числовым программным управлением для выбора блока подпрограмм процесса обработки
В работе оптимизирован процесс исследования коррекций при токарной обработке деталей на станке с ЧПУ, предложены методы повышения эффективности процесса обработки при программировании используя метод типовых подпрограмм, создания базы данных типовых подпрограмм.
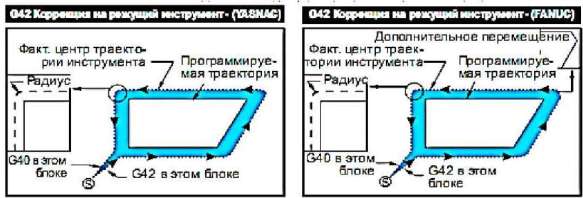
Рисунок 12 - Схема программной настройки коррекции параметров инструмента
В ходе исследования разработаны этапы программирования процесса обработки деталей и заготовок на станках с ЧПУ с учетом коррекции, возникающей в условиях мелкосерийного производства, предложен метод внедрения в программный код, который показан на рисунке 12, дополнительных параметров обработки, позволяющих значительно повысить эффективность управляющей программы. Результаты исследования приведены в таблице 5.
Таблица 5 - Параметры режущего инструмента при обработке детали на станке с числовым программным управлением
Код инструмента |
Инструмент |
|
Вспомогательный инструмент |
Координаты настройки |
Блок/ Код подпрограммы |
ф, град |
фі, град |
К, мм |
1, мм |
матери ал |
Код державки |
Код сборки |
А |
В |
01 |
Резец подрезно-проходной с трехгранной пластинкой |
95 |
5 |
1-0,2 |
40 |
ВК6, Т15К6 |
01 |
01;03 02;04 |
172 172 |
192 153 |
кА7 кА2 010101010104 |
02 |
Резец подрезно-проходной с трехгранной пластинкой левый |
95 |
5 |
1-0,2 |
40 |
ВК6, Т15К6 |
01 |
05;07 06;08 |
172 172 |
192 153 |
кА6,кА7 020101020108 |
03 |
Резец подрезно-проходной с четттрехгранной пластинкой |
45 |
45 |
1-0,2 |
40 |
ВК6, Т15К6 |
01 |
01-04 |
172 |
173 |
кА3,кА2 030101030104 |
17 |
Резец резьбовой |
|
|
|
30 |
ВК6, Т15К6 |
01 |
01-04 |
162 |
180 |
кА4 170101170104 |
20 |
Сверло |
118 |
|
|
114 |
Р18 |
02 |
09;10 |
276 |
174 |
кА3,кА5 200207200210 |
21 |
Сверло |
118 |
|
|
158 |
Р18 |
03 |
09;10 |
320 |
174 |
кА2 210305210310 |
22 |
Сверло |
118 |
|
|
192 |
Р18 |
04 |
09;10 |
354 |
174 |
кА2 220403220410 |
23 |
Сверло |
118 |
|
|
219 |
Р18 |
05 |
09;10 |
381 |
174 |
кА1 230502230510 |
В ходе выполнения работ разработаны и предложены методы и алгоритмы оптимизации процесса обработки деталей и заготовок на станке с ЧПУ, обеспечивающие эффективность процесса.
В заключении приводятся основные результаты диссертационного исследования.
ОСНОВНЫЕ РЕЗУЛЬТАТЫ И ВЫВОДЫ:
Основные научные выводы, теоретические и практические результаты заключаются в следующем:
1. Проведен анализ основных требований к процессу обработки деталей на станках с ЧПУ в условиях мелкосерийного производства, определены основные показатели оптимизации процесса обработки деталей и заготовок на станках с ЧПУ, а также зависимость эффективности применения программного управления станком от концентрации и сложности процесса обработки детали на станке;
2. Проведен анализ основных критериев выбора параметров режимов резания, обеспечивающие оптимальную стойкость инструмента, определены основные принципы, применяемые при выборе параметров режима процесса резания при токарной обработке на станке с ЧПУ с учетом особенностей конструктивных и технологических параметров обрабатываемой детали;
3. Разработан алгоритм решения задачи линейного программирования симплекс-методом при выборе наиболее оптимальных параметров управления процессом обработки (резания) для повышения эффективности;
4. Предложен алгоритм построения классификационного ряда поправки для обработки деталей на станках с ЧПУ исходя из технологических возможностей станка и трудоемкости составления программного кода для изготовления детали в условиях мелкосерийного производства;
5. Разработана математическая модель процесса программируемой обработки деталей на станках с ЧПУ для достижения высокой точности, которая в соответствии с проведенными исследованиями в условиях промышленного производства может обеспечить точное соблюдение надежного заданного периода полной стойкости режущего инструмента;
6. Разработаны новые методы контроля точности обработки деталей на станках с ЧПУ, основанные на математических свойствах рассеяния размеров деталей, обработанных при неизменных условиях и расположенных в возрастающем порядке с указанием частоты повторения и распределением размеров заготовок;
7. Разработан обобщенный алгоритм назначения переходов обработки отверстий на токарном станке с ЧПУ при программировании кода управляющей программы для автоматизации процесса обработки, алгоритм оптимизации обработки деталей и заготовок на станках с числовым программным управлением путем коррекции при программировании и обработке первой детали;
8. Результаты диссертации получили внедрение в производство. Разработанные алгоритмы и комплекс типовых программ приняты к использованию в ОАО НПО «Бином» (г. Владикавказ) с экономическим эффектом в 683 тыс. руб.
ОСНОВНЫЕ ПУБЛИКАЦИИ ПО РАБОТЕ
Публикации в ведущих рецензируемых научных журналах, включенных в перечень ВАК
1. Сидорчик Е.В. Повышение качества управляющих программ для изготовления деталей и заготовок на станках с числовым программным управлением // Известия Тульского государственного университета. Технические науки, №6(1), 2013. С.200-204.
2. Сидорчик Е.В. Повышение производительности работы станков с числовым программным управлением и точности обработки деталей // Науковедение. Электронный журнал, 2013, №4(17) [Электронный ресурс] - Москва, 2013. - Режим доступа: http ://naukovedenie.ru/PDF/68tvn413.pdf, свободный.
3. Сидорчик Е.В. К вопросу об эффективности использования станков с числовым программным управлением путем программирования первой детали // Системы управления и информационные технологии, №3(53), Воронеж, 2013. С. 91-95.
Публикации в других изданиях:
4. Сидорчик Е.В. К вопросу о повышении эффективности использования систем числового программного управления в промышленности // Современная наука: актуальные проблемы теории и практики (Естественные и технические науки), №7-8, Москва, 2011. С.25-29.
5. Сидорчик Е.В. Перспективные направления в расширении технологических возможностей обработки деталей на станках с числовым программным управлением // Современная наука: актуальные проблемы теории и практики (Естественные и технические науки), №7-8, Москва, 2013. С.30-34.
6. Сидорчик Е.В. Применение автоматического регулирования процесса обработки деталей на станках с числовым программным устройством для повышения эффективности // Журнал научных публикаций аспирантов и докторантов, №8, Курск, 2012. С.156-158.
7. Сидорчик Е.В. Повышение эффективности обработки деталей на станках с числовым программным управлением на технологическом этапе анализа и программирования // Научная перспектива, №8(42), Уфа, 2013. С.82-84.
8. Сидорчик Е.В. Оптимизация процесса резания в системах автоматизированного программирования для обработки на станках с числовым программным управлением // Международный научно-исследовательский журнал, №8(15), часть 2, Екатеринбург, 2012. С.60-62.
9. Мустафаев Г.А., Сидорчик Е.В. Использование датчиков адаптивного управления для повышения качества обработки деталей на станках с числовым программным управлением // Молодой ученый, №9(56), Чита, 2013. С.60-62.
10. Сидорчик Е.В. Особенности системного анализа и программирования для повышения эффективности процесса обработки деталей на станках с числовым программным управлением // Апробация, №6(9), Махачкала, 2011. С.24-27.
11. Сидорчик Е.В. Критерии повышения производительности обработки деталей на станках с числовым программным управлением // Материалы X Международной научно-практической конференции «Техника и технология: новые перспективы развития» (28.08.2013), Естественные и технические науки. - Москва: Изд. «Спутник +», 2013. С.53-57.
12. Сидорчик Е.В. Контроль, отладка и внедрение программ при оптимизации технологического процесса обработки на токарном станке с числовым программным управлением // Сборник материалов II Международной научно-практической конференции «Актуальные проблемы современной науки в 21 веке» (30.08.2013). -Махачкала: Изд. «Апробация», 2012. С.28-31.
13. Сидорчик Е.В. Новое в повышении эффективности обработки и повышении качества изготовления деталей на программируемых станках с числовым программным управлением // Материалы III Международной заочной научно-практической конференции «Наука вчера, сегодня, завтра» (21.08.2013). - Новосибирск: Изд. «СибАК», 2013. С.52-56.
|